When embarking on a construction project, understanding the breakdown of costs is crucial.
Typically, materials account for 65% to 80% of total construction expenses. This significant portion highlights the need for careful planning and budgeting, as the choice of materials can greatly impact the project’s overall cost and quality.
Labor costs also play an essential role, usually making up 20% to 35% of total expenses. These percentages can vary based on the complexity and scale of the project.
For new constructions, such as residential buildings or commercial spaces, knowing how to balance material and labor costs is key to ensuring both efficiency and profitability for construction companies.
Additionally, overhead costs can further influence these percentages, often affecting how projects are managed.
Components of Construction Costs

Construction costs can be divided into several key components. Each of these components plays a crucial role in the overall budget of a project. Understanding these elements helps in effective construction accounting and accurate cost estimation.
Material Costs
Material costs are a significant part of any construction project, often accounting for 40% to 60% of the total expenses.
These costs include essential construction materials such as plywood, concrete, steel, windows, doors, plumbing, and electrical systems.
High-quality materials can improve durability but may increase costs. For instance, energy-efficient windows might cost more upfront but save money on energy bills over time.
It’s important to carefully plan and source materials to manage the budget effectively. Factors like transportation and storage can also add to material costs, making it essential to consider these aspects during the planning phase.
Book Your Dream Vacation Today
Flights | Hotels | Vacation Rentals | Rental Cars | Experiences
Labor Costs
Labor costs encompass both direct and indirect expenses.
Direct labor costs refer to wages paid to workers directly involved in construction. This includes carpenters, electricians, and plumbers.
Depending on the region and complexity of the project, labor costs can vary significantly.
Indirect labor costs cover administrative salaries, benefits, and even professional services like legal or accounting help. In total, labor costs can represent 20% to 35% of the entire construction budget.
Managing these costs requires effective scheduling and workforce planning to avoid overruns. Efforts to train workers can also lead to improved efficiency and reduced expenses in the long run.
Overhead and Operating Costs
Overhead and operating costs are indirect costs associated with running a construction business.
These can include general overhead like administrative salaries, insurance premiums, marketing expenses, and equipment rental.
For new projects, these costs typically range from 10% to 20% of the total budget.
Accurate tracking of these expenses is vital for project management.
Such costs also cover depreciation of equipment and utility bills. Understanding and estimating these overheads helps in determining the final pricing for a construction project, ensuring all angles are considered for profitability.
Estimating and Managing Project Costs
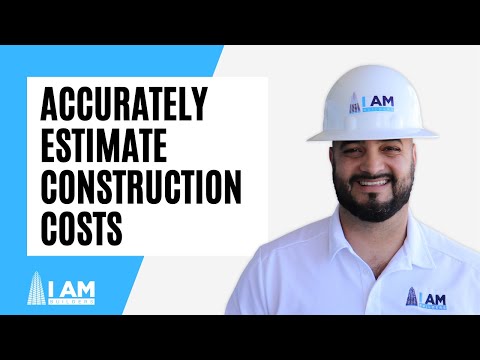
Estimating and managing construction project costs is crucial for staying on budget. This involves a detailed assessment of material costs and other expenses. By understanding these factors, project managers can make informed decisions throughout the construction process.
Construction Estimating
Effective construction estimating involves analyzing all components of a project to predict costs accurately.
Material costs typically make up a significant portion of these estimates. For instance, in a single-family home, material costs can range from 40% to 70% of the total budget.
Using construction estimating software streamlines this process. It allows managers to input costs for various materials, labor, and equipment.
This software facilitates quick adjustments based on market fluctuations or project changes, ensuring estimates remain relevant.
Accurate estimates also include taxes and expected profit margins, which play a critical role in overall funding.
Additionally, risk assessments must be conducted. This includes identifying potential unexpected costs, which could arise from weather delays or material shortages.
Additional Costs and Considerations
Beyond material costs, several additional factors impact the budget.
Maintenance costs and warranty expenses should also be included in the initial estimates. These are often overlooked but essential for long-term project sustainability.
Moreover, oversight through construction management is necessary to track expenditures. This helps ensure that costs align with the budget, allowing for early adjustments if needed.
Understanding indirect costs, like utility fees and equipment rentals, is also important.
Lastly, project managers should prepare for the possibility of unforeseen expenses. Having a contingency fund ensures that resources remain available without derailing the project timeline.
Book Your Dream Vacation Today
Flights | Hotels | Vacation Rentals | Rental Cars | Experiences