The Navistar Truck Assembly Plant, located in San Antonio, Texas, stands as a testament to modern manufacturing ingenuity.
This facility was designed to produce both electric and conventional trucks, showcasing a blend of innovation and sustainability in its architecture.
The plant includes four main buildings: a general assembly building, a logistics warehouse, a paint building, and a body shop, all crafted to optimize efficiency and streamline production processes.
With a total investment of around $250 million, the design prioritizes functionality while embracing advanced technology.
The layout facilitates a smooth flow of operations, vital for assembling Classes 6 to 8 trucks. The site’s strategic location in an undeveloped area enabled Navistar to create a purpose-built facility tailored specifically to its manufacturing needs, thus enhancing its competitive edge in the industry.
As readers delve into the architecture behind this impressive assembly plant, they will uncover how thoughtful design choices contribute to both productivity and environmental consciousness. This exploration reveals not only the importance of modern manufacturing facilities but also the architectural vision that shapes the future of the automotive industry.
History and Background of Navistar
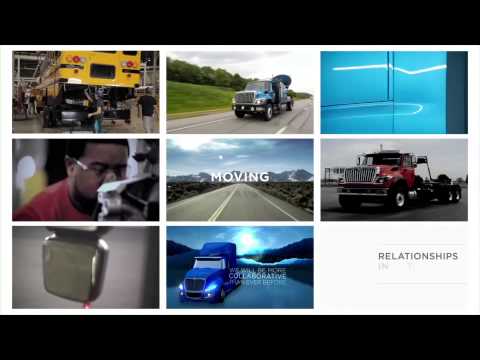
Navistar, known for its trucks and other commercial vehicles, has a rich history shaped by strategic decisions and market demands. Its journey includes significant investments and expansions, especially into Texas, reflecting its growth ambitions.
Navistar’s Evolution
Navistar’s roots go back to the 1830s, initially functioning under different names before becoming the International Harvester Company. In the late 20th century, it rebranded as Navistar International Corporation, focusing on engines and heavy-duty trucks.
In the early 2000s, Navistar faced challenges, including legal issues and market competition. Despite these hurdles, the company adapted by embracing new technologies and increasing efficiency in production.
In more recent years, Navistar entered into a partnership with Traton, a subsidiary of Volkswagen, which provided essential investment and resources for further expansion.
The Expansion into San Antonio
The decision to build a new assembly plant in San Antonio was a significant milestone for Navistar. The facility, constructed with a $250 million investment, is the first new truck plant in the United States in nearly 30 years.
This plant spans 970,000 square feet and is capable of producing both electric and conventional powertrain trucks. It not only reinforces Navistar’s commitment to innovation but also aims to meet growing demands for environmentally friendly vehicles.
The location in Texas allows Navistar to better serve its clients in the southwestern U.S. and to leverage the region’s skilled workforce and logistical advantages.
Strategic Location of the Plant

The strategic location of the Navistar Truck Assembly Plant plays a vital role in its operations. The site benefits from excellent logistics and connectivity, as well as offering advantages to the local San Antonio region.
Logistics and Connectivity
Located in San Antonio, Texas, the assembly plant sits at a central point for transport and distribution. This location enables easy access to major highways, such as I-10 and I-35, facilitating the quick movement of raw materials and finished products.
The proximity to the San Antonio Logistics Center enhances efficiency. Supply chain management is simplified, as suppliers can deliver components with reduced transit times. This directly impacts production speed and reduces costs.
Additionally, nearby rail connections provide alternative transport options, further boosting the plant’s logistical capabilities. This integrated transport network ensures that Navistar can respond swiftly to market demands.
Benefit to the San Antonio Region
The establishment of the assembly plant brings significant economic benefits to the San Antonio area. It creates numerous job opportunities, directly impacting local employment rates. Skilled labor from the surrounding communities can find stable jobs, which in turn supports local businesses.
Moreover, the presence of a major manufacturing facility promotes infrastructure improvements. Roads, utilities, and services may receive upgrades to accommodate increased traffic and demand.
This facility contributes to San Antonio’s economic growth and positions it as an important player in the automotive industry. Increased business activity can attract further investments in the region, making it a key area for future development, including more projects in regional architecture.
Architectural Design and Layout
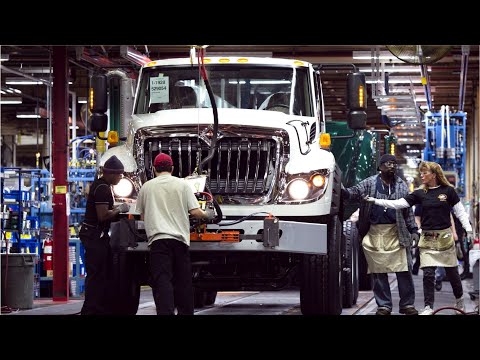
The architectural design and layout of the Navistar Truck Assembly Plant are key to its efficiency and functionality. This section examines the assembly line design, the application of lean manufacturing principles, and the sustainability features incorporated into the building.
Assembly Line Design
The assembly line at Navistar is strategically designed for optimal workflow. It features a linear layout that minimizes movement and maximizes operational efficiency. Each station is clearly defined, allowing workers to focus on specific tasks while ensuring a smooth flow of vehicles through the assembly process.
Key design elements include:
- Modular Workstations: Flexibility to adapt to changing production needs.
- Ergonomic Considerations: Workstations designed for comfort to reduce strain on workers.
- Clear Pathways: This reduces congestion and enhances safety.
The thoughtful arrangement of the assembly line allows for quick adjustments and efficient production rates, essential for meeting market demands.
Lean Manufacturing Principles
Lean manufacturing principles guide the operations within the Navistar plant. These principles focus on reducing waste while maximizing productivity.
Key features of lean manufacturing implemented include:
Book Your Dream Vacation Today
Flights | Hotels | Vacation Rentals | Rental Cars | Experiences
- Just-In-Time Production: Reduces inventory costs by producing only what is needed when it is needed.
- Continuous Improvement (Kaizen): Encourages ongoing, small changes that lead to significant enhancements over time.
- Cross-Training Employees: This creates flexibility in the workforce, allowing staff to perform multiple tasks.
These principles not only enhance productivity but also foster a culture of efficiency and quality among employees.
Sustainability Features
Sustainability is a cornerstone of the Navistar Truck Assembly Plant’s design. The architecture incorporates various features aimed at minimizing the environmental impact of operations.
Sustainable practices include:
- Energy-Efficient Lighting: LED lighting is used throughout the plant to reduce energy consumption.
- Rainwater Harvesting Systems: These systems capture rainwater for use in non-potable applications, leading to decreased water usage.
- Recycled Materials: Construction materials are selected based on their recyclability and low environmental impacts.
By focusing on sustainability, Navistar not only complies with regulations but also demonstrates a commitment to environmental stewardship.
Advanced Technology Center

The Advanced Technology Center plays a crucial role in Navistar’s innovation strategy. This facility focuses on integrating new technologies into truck assembly processes and harnessing data for improved operations. The incorporation of AI, electrification, and cloud analytics helps streamline manufacturing and creates a more responsive production environment.
Emerging Technologies Integration
Emerging technologies are central to the operations at the Advanced Technology Center. This facility incorporates AI to optimize manufacturing processes and enhance quality control. For instance, AI-powered robotics work alongside human assembly lines to ensure precision and efficiency.
Additionally, the facility explores electrification in truck manufacturing. This includes developing electric vehicle models and integrating sustainable energy solutions into the production system.
Cloud Analytics and Connectivity
Cloud analytics form a significant part of the Advanced Technology Center’s capabilities. By utilizing cloud-based systems, Navistar collects and analyzes vast amounts of data generated during production. This analysis provides insights into operational efficiency, helping the company make informed decisions.
Furthermore, connected machinery within the plant enables real-time data sharing across devices. This connectivity ensures maintenance needs are addressed promptly, reducing downtime. Leveraging cloud analytics supports continuous improvement in manufacturing processes, aligning with Navistar’s mission for innovation and excellence in the truck assembly industry.
Manufacturing Operations
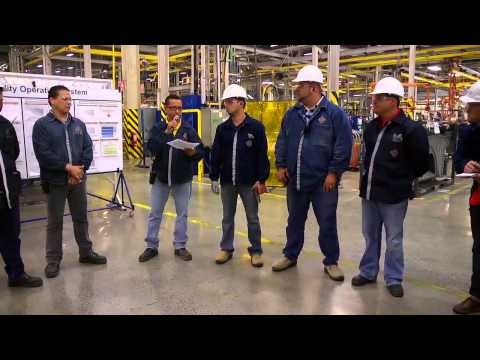
Navistar’s manufacturing operations are designed for efficiency and quality. The processes in the Body Shop, Paint Shop, and General Assembly Shop utilize advanced techniques and lean manufacturing principles to streamline production. Each area focuses on precision and productivity, ensuring high standards for both conventional and electric trucks.
Body Shop Processes
The Body Shop at Navistar plays a crucial role in constructing the vehicle’s framework. This area uses automated machinery for tasks like welding, which ensures consistent strength and quality.
Operators follow lean manufacturing principles, reducing waste and improving workflow. The team also integrates just-in-time inventory systems, ensuring that materials arrive as needed, which minimizes storage and costs.
In addition, safety protocols are strictly maintained. Workers wear protective gear, and safety sensors are installed on machinery to prevent accidents.
Paint Shop Techniques
In the Paint Shop, vehicles are treated with advanced coating methods that enhance durability and appearance. Navistar employs a multi-step process that includes surface preparation, primer application, and finishing coats.
Environmentally friendly paints are utilized to adhere to regulations and reduce environmental impact. The shop features automated spray booths that ensure even coverage and minimize overspray.
Quality control is a significant part of this process. Each vehicle is inspected for paint defects, ensuring that only flawless products move to the next stage.
General Assembly Shop
The General Assembly Shop is where the assembly of the trucks comes together. Utilizing a flexible assembly line, this area allows for the simultaneous production of conventional and electric trucks.
Workers are trained in multiple skills, enabling them to switch between tasks as needed. This approach enhances efficiency and reduces downtime.
Lean manufacturing principles guide operations here as well, focusing on minimizing waste and optimizing processes.
The shop includes quality checkpoints, where each vehicle is tested to ensure it meets Navistar’s production standards. This dedication to quality ensures that customers receive reliable and robust trucks.
Product Range and Innovation

Navistar’s Truck Assembly Plant stands out for its commitment to innovation and a diverse product range. The facility not only manufactures traditional internal combustion trucks but also embraces cutting-edge electric technology.
International eMV Series
The International eMV Series is designed to cater to the growing demand for eco-friendly transportation solutions. This product line includes electric trucks suitable for urban and regional deliveries.
The eMV trucks feature a low floor for easy access and advanced safety systems. These vehicles support both local and federal emissions regulations, highlighting their importance in sustainable logistics.
Moreover, the eMV Series offers various configurations, making it adaptable for different business needs. Its design combines functionality with a sleek aesthetic, appealing to forward-thinking companies focusing on sustainability.
Powertrains and Electric Trucks
Navistar’s focus on Powertrains includes internal combustion engines (ICE) and electric drive systems. The plant manufactures Class 6 to Class 8 trucks, allowing for flexibility across various industries, from construction to food distribution.
The introduction of electric trucks marks a significant shift in the manufacturing approach. Electric trucks aim for reduced operational costs and lower emissions, supporting businesses’ goals for sustainability.
Navistar engineers combinations of advanced gasoline and diesel powertrains alongside electric alternatives. This variety ensures customers can select solutions tailored to their unique operational needs, contributing to a more diverse marketplace.
Zero-Emission Components
At the heart of Navistar’s innovation lies its Zero-Emission Components. These parts are essential for the creation of fully electric vehicles and play a vital role in reducing the environmental impact of transportation.
Navistar focuses on integrating advanced batteries, electric motors, and energy-efficient technologies into their designs. This approach helps customers transition away from traditional fuel sources.
Furthermore, Navistar is committed to continuous improvement of these components, ensuring they meet the latest industry standards for efficiency and performance. By developing these zero-emission solutions, the company showcases its dedication to creating reliable and sustainable transportation options.
Sustainable Practices and Goals

Navistar’s new assembly plant in San Antonio focuses on integrating sustainable practices into its design and operations. The facility aims to minimize environmental impact while adopting new technologies to promote sustainability.
This commitment is evident in its environmental initiatives and efforts towards electrification and autonomous technologies.
Environmental Initiatives
Navistar has incorporated various environmental initiatives within its San Antonio plant. This includes a goal of reducing energy intensity by 20% by 2030.
Such measures are part of a broader effort to lower the carbon footprint of the manufacturing process.
Book Your Dream Vacation Today
Flights | Hotels | Vacation Rentals | Rental Cars | Experiences
- The plant uses green building practices to enhance energy efficiency.
- Water usage is optimized through recycling and conservation strategies.
- Waste generated during production is minimized and managed effectively.
These practices support Navistar’s vision of becoming a leader in sustainable manufacturing. By setting benchmarks for environmental performance, they pave the way for future advancements in the trucking industry.
Electrification and Autonomous Technologies
Alongside its environmental goals, the plant is advancing electrification and exploring autonomous technologies. The adoption of electric vehicles is a key strategy for reducing emissions in production and transportation.
- The facility focuses on producing electric and hybrid models. This shift aligns with global trends towards cleaner transport solutions.
- Autonomous technologies are being incorporated to enhance efficiency and safety in manufacturing processes.
By integrating these technologies, Navistar aims not only to boost operational efficiency but also to contribute positively to a sustainable future in transportation. These innovations will play a significant role in transforming the industry towards greener solutions.
The Impact on Commercial Trucking

The new Navistar assembly plant significantly influences the commercial trucking sector. Innovations in logistics and advancements in Class 6-8 vehicles are key areas transforming how trucks are produced and delivered.
Improvements in Logistics
The location and design of the San Antonio plant enhance logistics for commercial trucking. With a focus on Industry 4.0 concepts, the facility integrates digital technology to streamline operations.
This includes advanced inventory management systems that reduce downtime and improve efficiency.
By using real-time data analytics, Navistar can better forecast demand and manage supply chains.
Reduced travel distances for parts also lower transportation costs and emissions. These improvements lead to quicker turnaround times, allowing companies to meet customer demands more efficiently.
Class 6-8 Vehicles Advancements
The plant is designed to manufacture Class 6-8 vehicles, which are essential for commercial trucking. This includes both electric and conventional powertrains, promoting a shift towards sustainable options.
Navistar’s focus on efficiency and performance includes lighter materials and improved aerodynamics in truck design. These advancements contribute to better fuel efficiency and lower operating costs for trucking companies.
Electric models are particularly significant as they address environmental concerns. They can help companies meet regulatory requirements while also appealing to environmentally conscious customers.
With these innovations, the impact on commercial trucking is substantial, pushing the industry towards a more sustainable and efficient future.
Economic Implications and Industry Impact

The Navistar Truck Assembly Plant in San Antonio represents a significant investment in the local economy and the commercial trucking industry. Its construction has led to job creation and strengthened ties across supply chains. The plant’s advanced architecture and technology also position it as a driver for innovation in manufacturing practices.
Job Creation and Market Influence
The new plant has generated numerous jobs, significantly impacting the local workforce. An estimated 1,000 direct jobs are linked to operations at the facility.
This development supports a range of positions, from assembly line workers to management roles.
Additionally, the economic ripple effect includes thousands of indirect jobs in related sectors. The demand for services, including logistics and maintenance, creates opportunities for local businesses.
The influx of workers also stimulates the San Antonio economy, increasing demand for housing, retail, and services.
The plant’s presence enhances San Antonio’s reputation as a hub for commercial trucking, attracting further investment from related industries. This strategic positioning can lead to job stability and growth in the region.
Collaboration with Suppliers and OEMs
Navistar’s San Antonio plant emphasizes collaboration with suppliers and original equipment manufacturers (OEMs).
By adopting advanced manufacturing practices, it drives efficiencies in the supply chain.
The plant’s design incorporates a technology-oriented approach, enabling seamless communication between systems and suppliers.
This integration ensures timely delivery of parts and reduces production delays.
Navistar aims to maintain strong relationships with local and national suppliers, enabling a robust network for parts and materials.
Furthermore, partnerships with OEMs help drive innovation and development in truck manufacturing.
This collaboration is crucial for meeting industry standards and evolving customer needs.
Overall, these relationships position Navistar as a key player in the future of the commercial trucking industry.
Book Your Dream Vacation Today
Flights | Hotels | Vacation Rentals | Rental Cars | Experiences