Understanding the costs involved in construction projects is vital for anyone interested in the building industry.
Typically, material costs make up about 65% to 80% of the total expenses in construction. This significant percentage highlights how crucial the choice of materials is, whether in residential constructions like single-family homes or in nonresidential projects such as office buildings.
Construction companies constantly face fluctuations in material prices, which can impact their overall budget and project timeline.
Alongside material costs are labor costs, which usually account for about 20% to 35% of total expenses. This blend of costs is essential for managing finances in any construction project and influences decision-making from project planning to execution.
When embarking on a building project, understanding these percentages can help stakeholders make informed choices. From choosing the right materials to finding skilled labor, these factors are interconnected in achieving successful construction outcomes.
Readers interested in maximizing their construction budgets will find this exploration of material costs both enlightening and practical.
Understanding Construction Material Costs
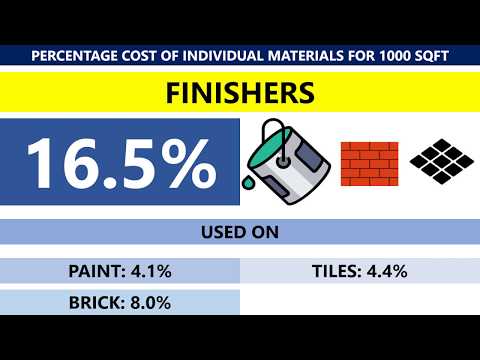
Construction material costs play a crucial role in determining the overall expenses of any building project.
These costs fluctuate based on various factors, including market demand, availability, and current economic conditions.
Book Your Dream Vacation Today
Flights | Hotels | Vacation Rentals | Rental Cars | Experiences
Components and Pricing of Construction Materials
Construction materials include items such as steel, concrete, wood, and roofing products. Each of these materials has different pricing structures influenced by their specific market dynamics.
For instance, iron and steel have seen significant price increases recently, with changes attributed to production costs and demand.
Common Material Costs:
- Steel and Iron: Highly variable, often affected by global demand.
- Concrete Products: Prices influenced by raw ingredients and transport costs.
- Plywood: Prices can rise in tandem with timber costs due to market conditions.
The choice of materials impacts both costs and project timelines, making it essential for builders to keep track of current prices.
Assessing the Impact of Inflation and PPI
Inflation directly affects material costs, which can lead to significant price fluctuations over time.
The Producer Price Index (PPI) measures changes in prices producers receive for their goods, including construction materials.
For example, an increasing PPI indicates that manufacturers are raising prices, which ultimately affects consumers and builders.
Historical data shows that during periods of high inflation, materials like roofing and plywood experienced sharp price increases.
Monitoring these trends helps in planning budgets effectively. By understanding these price changes, builders can better manage costs and avoid budget overruns.
Breaking Down Labor Costs in Construction
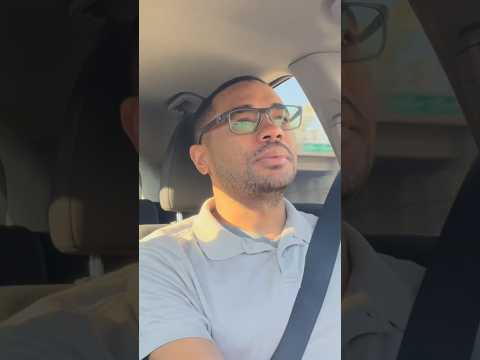
Labor costs are a significant part of construction expenses.
These costs can be split into two main categories: direct and indirect labor costs. Understanding these components helps in estimating project expenses more accurately.
Direct and Indirect Labor Costs
Direct labor costs include wages paid to workers who are directly involved in a construction project. This can cover various roles such as carpenters, electricians, and laborers. These costs are straightforward and essential to calculate as they directly affect the total project costs.
Indirect labor costs, on the other hand, cover expenses not directly tied to specific project tasks. These can include payroll taxes, benefits, and other overhead expenses related to staff.
It is important for a general contractor to factor both types of labor costs to grasp the true expense of construction projects.
For example, if a worker earns $25 per hour, the direct cost for eight hours of work would be $200. If indirect costs, like benefits, add another $10 per hour, the total labor cost would rise to $300 for that day.
Determining Labor Costs with Unit Pricing Method
The unit pricing method is a common approach to assess labor costs in construction projects. This method assigns a price to specific units of work, such as per square foot or per hour.
For example, a contractor might determine that laying a foundation costs $10 per square foot. If the foundation is 1,000 square feet, the labor cost would total $10,000. This method gives a clear view of how labor impacts overall project costs.
It’s essential to apply the rule of two when calculating these costs. This rule suggests that the total labor cost includes both direct and indirect costs. Understanding this helps contractors create more accurate budgets and manage expenses effectively during construction projects.
This clarity in labor costs aids in making informed decisions on pricing and resource allocation.
Book Your Dream Vacation Today
Flights | Hotels | Vacation Rentals | Rental Cars | Experiences